
The $600 piece of aluminum that connects the transmission and engine on a Softail is marked so I can have it cut in half. Maybe I can make a piece of motorcycle art from the front half. The BDL belt drive kit has enough pieces left to make a really nice bookend.
Several of the motor mount holes on the engine are stripped. It appears that some of the bolts have a different thread pitch than the engine takes. I thought I kept the bolts separate, but obviously all of them will need to be chased with a tap. Some will need to be retapped, but all of them need to be correct before the engine gets bolted down for the last time.
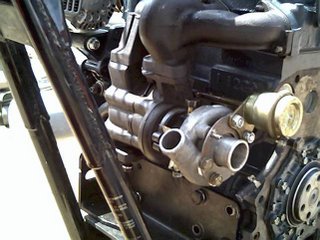
You can see one of the bolts for the exhaust next to the frame rail. Exhaust plumbing should be easy enough. It simply needs a pipe that goes down and to the back of the bike.
This week the plan is to identify and begin connecting some of the other items. Before now, simply putting the engine in the right place was a challenge. Now I can concentrate on some of the other items.