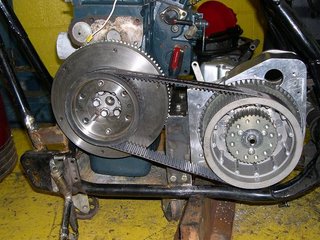
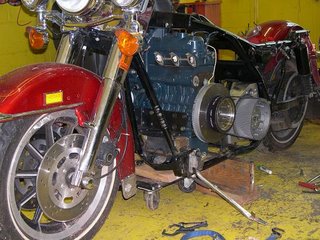
The motor mounts have the first set of holes drilled. The flywheel is back from the machine shop, the pulley is attached. I lined everything up and scored the other side of the motor mounts so those holes can be drilled. The Heim joints and turn-buckles used to position the Harley engine were recycled to keep the belt drive aligned. The mounts for those have been built and only a few bolts need to be purchased to keep the engine in permanent alignment. The pictures were taken before the Heim joints were installed. The screwdriver in the picture serves as a wedge to keep things lined up for measurements.
The top of the intake manifold has been cut down and capped. The plug was removed from the end of the manifold. A one inch copper street elbow still needs to be epoxied to the manifold. Once the engine is bolted down, that plumbing can be completed.
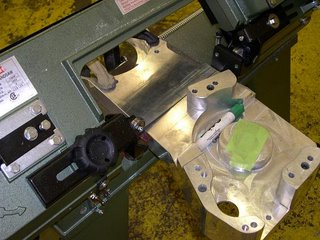
0 Comments:
Post a Comment
<< Home